BUSINESS
【生産計画の最適化】効率的な製造プロセスを実現する方法
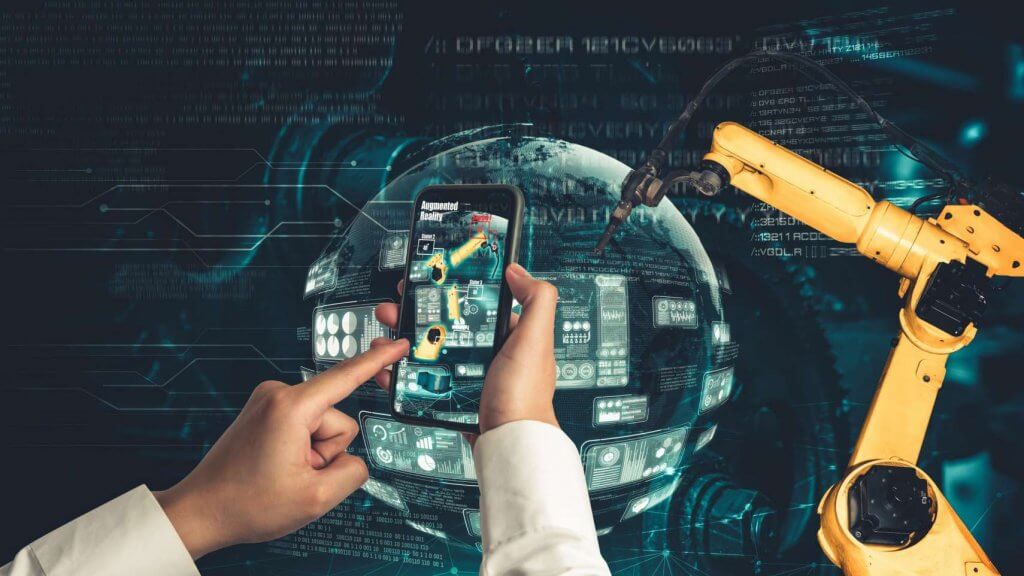
目次
この記事では、生産計画の最適化について包括的に解説します。効率的な製造プロセスを実現するための重要性、基本概念、手法、ツール、テクノロジーの活用方法を学ぶことができるでしょう。需要予測、在庫管理、スケジューリング、リソース配分など、生産計画最適化の具体的な要素を理解し、AIやIoTなどの最新技術の活用法も解説します。
さらに、最適化の実施手順やベストプラクティス、直面する課題とその対策についても詳しく説明します。本記事を読むことで、生産性向上、コスト削減、品質改善といった具体的な成果を得るための実践的な知識が身につきます。トヨタ生産方式やカイゼン活動など、日本企業の成功事例も交えながら、製造業における競争力強化の鍵となる生産計画最適化の全容を把握できます。
1. 生産計画最適化の重要性と基本概念
生産計画の最適化は、製造業において効率的な生産プロセスを実現するための重要な要素です。本章では、生産計画最適化の基本概念や重要性について詳しく解説します。
1.1 生産計画最適化とは何か
生産計画最適化とは、限られたリソース(人員、設備、原材料など)を最大限に活用し、生産効率を高めながらコストを抑え、納期を守るための計画立案プロセスです。
具体的には、需要予測、在庫管理、生産スケジューリング、リソース配分などを総合的に考慮し、最適な生産計画を策定することを指します。
経済産業省の報告によると、日本の製造業の生産性向上が急務となっており、生産計画の最適化はその重要な施策の一つとして挙げられています。
1.2 生産計画最適化がもたらす利点
生産計画を最適化することで、以下のような利点が得られます。
- 生産効率の向上
- 在庫の適正化
- 納期遵守率の向上
- コスト削減
- リソースの有効活用
- 柔軟な生産体制の構築
これらの利点は、企業の競争力強化や収益性向上に直結します。しかしながら現状では、日本能率協会コンサルティングの調査によると、日本の製造業では既存製品で価格転嫁ができず、グローバル競争に敗退してしまう可能性があり、生産性向上が必須と提言されています。
1.3 生産計画最適化の主要な要素
生産計画最適化を実現するためには、以下の要素を考慮する必要があります。
要素 | 説明 |
---|---|
需要予測 | 将来の需要を正確に予測し、適切な生産量を決定する |
在庫管理 | 適正な在庫レベルを維持し、過剰在庫や欠品を防ぐ |
生産能力分析 | 設備や人員の生産能力を把握し、最適な生産量を決定する |
リードタイム管理 | 各工程のリードタイムを把握し、納期を遵守する |
コスト最適化 | 生産コストを最小化しつつ、品質を維持する |
これらの要素を総合的に考慮し、バランスの取れた生産計画を立案することが重要です。近年では、AIや機械学習技術を活用して、これらの要素をより精緻に分析し、最適な生産計画を導き出す企業が増えています。
1.3.1 生産計画最適化の実施手順
生産計画最適化を実施する際の一般的な手順は以下の通りです。
- 現状分析:現在の生産プロセスや課題を把握する
- 目標設定:最適化によって達成したい目標を明確にする
- データ収集:需要予測、生産能力、在庫状況などのデータを収集する
- 最適化モデルの構築:収集したデータを基に最適化モデルを作成する
- シミュレーション:様々なシナリオでシミュレーションを行い、最適解を見出す
- 計画の実行:最適化された生産計画を実行に移す
- モニタリングと改善:実行結果を分析し、継続的に改善を図る
この手順を繰り返し実施することで、より精度の高い生産計画最適化が可能となります。
生産計画最適化は、製造業の競争力強化に不可欠な要素です。次章では、生産計画最適化のための具体的な手法やツールについて詳しく解説します。
2. 生産計画最適化のための手法とツール
生産計画の最適化は、製造業にとって非常に重要な課題です。適切な手法とツールを活用することで、生産効率の向上、コスト削減、納期短縮などの大きな効果が期待できます。ここでは、生産計画最適化のための主要な手法とツールについて詳しく解説します。
2.1 需要予測と在庫管理の最適化
需要予測と在庫管理は、生産計画の基礎となる重要な要素です。精度の高い需要予測を行うことで、過剰在庫や欠品を防ぎ、適正な生産量を維持することができます。
2.1.1 需要予測の手法
- 時系列分析: 過去のデータから傾向やパターンを分析し、将来の需要を予測
- 回帰分析: 需要に影響を与える要因を特定し、その関係性から予測を行う
- 機械学習: AIを活用して複雑なパターンを学習し、高精度な予測を実現
2.1.2 在庫管理の最適化手法
- ABC分析: 商品を重要度別に分類し、効率的な在庫管理を行う
- EOQ(経済的発注量)モデル: 最適な発注量と発注タイミングを算出
- ジャストインタイム(JIT): 必要な時に必要な量だけ生産・調達する方式
これらの手法を組み合わせることで、より精度の高い需要予測と効率的な在庫管理が可能になります。例えば、三井物産株式会社では、AIを活用した需要予測システムを導入し、サプライチェーン最適化に取り組んでいます。
2.2 生産スケジューリングの効率化
生産スケジューリングは、限られたリソースを最大限に活用し、効率的な生産を実現するための重要な要素です。適切なスケジューリング手法を用いることで、生産リードタイムの短縮や設備稼働率の向上が可能になります。
2.2.1 主なスケジューリング手法
手法 | 特徴 | 適用例 |
---|---|---|
ガントチャート | 視覚的に作業の進捗状況を管理できる | 小規模な生産ラインの管理 |
クリティカルパス法(CPM) | プロジェクト全体の所要時間を最小化する | 大規模プロジェクトの工程管理 |
ジョブショップスケジューリング | 複数の工程や機械を考慮した最適化を行う | 多品種少量生産の工場 |
これらの手法を効果的に活用するためには、適切なソフトウェアツールの導入が不可欠です。例えば、富士通株式会社の生産スケジューリングシステムは、AIを活用して複雑な生産ラインの最適化を実現しています。
2.3 リソース配分の最適化
生産計画の最適化において、人員、設備、材料などのリソースを効率的に配分することは非常に重要です。適切なリソース配分により、生産性の向上とコスト削減を同時に達成することができます。
2.3.1 リソース配分最適化の手法
- 線形計画法: 制約条件下で目的関数を最大化または最小化する数学的手法
- 遺伝的アルゴリズム: 進化の過程を模倣し、複雑な問題の最適解を探索する手法
- シミュレーション: 仮想環境で様々なシナリオを検証し、最適な配分を見出す
これらの手法を活用することで、人員配置の最適化、設備稼働率の向上、原材料の効率的な使用などが可能になります。例えば、NECのシステムでは、生産計画の立案時間を大幅に短縮し、生産性を向上させることができます。
生産計画の最適化は、これらの手法とツールを適切に組み合わせ、自社の生産環境に合わせてカスタマイズすることが重要です。また、継続的な改善と最新技術の導入により、さらなる効率化と競争力の強化が可能になります。
3. 生産計画最適化のためのテクノロジー活用
生産計画の最適化において、最新のテクノロジーを活用することは非常に重要です。AIや機械学習、IoT、ビッグデータ分析、クラウドコンピューティングなどの先端技術を導入することで、生産プロセスの効率化と精度向上を図ることができます。ここでは、生産計画最適化に活用できる主要なテクノロジーについて詳しく見ていきましょう。
3.1 AIと機械学習の活用
人工知能(AI)と機械学習は、生産計画の最適化において非常に強力なツールとなっています。これらのテクノロジーを活用することで、以下のような利点が得られます。
- 需要予測の精度向上
- 生産スケジュールの最適化
- 異常検知と予防保全
- 品質管理の強化
AIによる需要予測では、過去の販売データや市場動向、天候情報などの多様なデータを分析し、より正確な将来の需要を予測することができます。これにより、過剰生産や在庫不足のリスクを軽減し、効率的な生産計画を立てることが可能になります。
機械学習アルゴリズムを用いた生産スケジュールの最適化では、生産ラインの稼働状況、原材料の在庫状況、納期などの様々な制約条件を考慮しながら、最も効率的な生産スケジュールを自動的に生成することができます。これにより、人手による試行錯誤を大幅に削減し、より短時間で最適な生産計画を立案することが可能になります。
NECのAIソリューションでは、製造業向けのAI活用事例が多数紹介されており、実際の導入効果を確認することができます。
3.2 IoTとビッグデータの統合
IoT(Internet of Things)技術とビッグデータ分析の統合は、生産計画の最適化に大きな変革をもたらしています。生産設備やセンサーからリアルタイムで収集されるデータを分析することで、以下のような効果が期待できます。
- 生産ラインの稼働状況のリアルタイムモニタリング
- 設備の予防保全と稼働率の向上
- エネルギー消費の最適化
- サプライチェーン全体の可視化と最適化
IoTセンサーによるリアルタイムデータ収集により、生産ラインの稼働状況や設備の状態をリアルタイムで把握することができます。これにより、生産計画の微調整や突発的な問題への迅速な対応が可能になります。
収集されたビッグデータを分析することで、予測型メンテナンスを実現し、設備の故障を事前に予測して計画的なメンテナンスを行うことができます。これにより、突発的な設備停止を防ぎ、生産計画の安定性を高めることができます。
日立製作所のLumadaソリューションでは、IoTとビッグデータ分析を統合した製造業向けのソリューションが提供されており、具体的な導入事例も紹介されています。
3.3 クラウドベースの生産管理システム
クラウドベースの生産管理システムは、生産計画の最適化において重要な役割を果たしています。クラウドシステムを活用することで、以下のようなメリットが得られます。
- リアルタイムでの情報共有と協業
- スケーラビリティと柔軟性の向上
- コスト削減とセキュリティの強化
- データの一元管理と分析の効率化
クラウド上での情報共有により、生産計画に関わる全ての部門や取引先との間で、リアルタイムでの情報共有と協業が可能になります。これにより、サプライチェーン全体での最適化が実現し、生産計画の精度向上につながります。
また、クラウドシステムのスケーラビリティと柔軟性により、生産規模の変動や新たな生産拠点の追加にも柔軟に対応することができます。これは、グローバルな生産ネットワークを持つ企業にとって特に重要な利点となります。
Microsoft Cloud for Manufacturingは、製造業向けのクラウドベースソリューションの一例で、生産管理から需要予測まで幅広い機能を提供しています。
3.3.1 クラウドベース生産管理システムの主要機能
機能 | 概要 |
---|---|
生産計画立案 | 需要予測データを基に最適な生産計画を立案 |
在庫管理 | リアルタイムでの在庫状況把握と最適化 |
品質管理 | 生産ラインでの品質データ収集と分析 |
設備管理 | 設備の稼働状況モニタリングと予防保全 |
サプライチェーン管理 | 取引先との情報共有と連携強化 |
これらのテクノロジーを適切に組み合わせ、自社の生産プロセスに最適化して導入することで、生産計画の精度向上と効率化を実現することができます。ただし、テクノロジーの導入には適切な戦略と段階的なアプローチが必要であり、社内の体制整備や人材育成も併せて行うことが重要です。
4. 生産計画最適化の実施手順とベストプラクティス
生産計画の最適化は、製造業において効率性と生産性を向上させるための重要なプロセスです。以下では、生産計画最適化の実施手順とベストプラクティスについて詳しく解説します。
4.1 現状分析と目標設定
生産計画最適化の第一歩は、現状の生産プロセスを詳細に分析し、明確な目標を設定することです。
4.1.1 現状分析の手法
- 生産ラインの稼働率分析
- ボトルネックの特定
- 在庫レベルの評価
- 納期遵守率の確認
データ駆動型の意思決定を行うために、過去の生産データを詳細に分析することが重要です。日本能率協会コンサルティングによると、年次・月次・週次・日次といった日程・時間軸を基軸に、何をいくつつくるかということと、ものをつくるために必要となる生産の諸要素(人、設備、材料)を計画し統制することとあります。
4.1.2 目標設定のポイント
- 具体的で測定可能な目標を設定
- 短期・中期・長期の目標を明確に区分
- 全社的な経営目標との整合性確保
目標設定においては、SMART基準(Specific, Measurable, Achievable, Relevant, Time-bound)を活用することが効果的です。
4.2 最適化戦略の策定
現状分析と目標設定が完了したら、次に具体的な最適化戦略を策定します。
4.2.1 主要な最適化戦略
戦略 | 概要 | 期待効果 |
---|---|---|
リーン生産方式の導入 | ムダを徹底的に排除し、ジャストインタイムの生産を実現 | 在庫削減、リードタイム短縮 |
需要予測の精度向上 | AIを活用した高精度な需要予測モデルの構築 | 過剰生産の防止、機会損失の削減 |
柔軟な生産ラインの構築 | 多品種少量生産に対応できる生産ライン設計 | 生産効率の向上、リードタイムの短縮 |
テクノロジーの活用は、生産計画最適化において重要な役割を果たします。経済産業省が推進するスマート製造は、IoTやAIを活用した生産性向上を目指しています。
4.3 段階的な導入とモニタリング
最適化戦略を一度に全面導入するのではなく、段階的に導入し、効果を継続的にモニタリングすることが重要です。
4.3.1 段階的導入のステップ
- パイロットプロジェクトの実施
- 特定の生産ラインや製品カテゴリーでテスト導入
- 課題の洗い出しと改善策の検討
- 成功事例の水平展開
- パイロットプロジェクトの成果を他部門へ展開
- ベストプラクティスの共有と標準化
- 全社的な展開
- 段階的に全生産ラインへ展開
- 継続的な改善サイクルの確立
4.3.2 効果的なモニタリング手法
- KPI(重要業績評価指標)の設定と定期的な測定
- リアルタイムモニタリングシステムの導入
- 定期的なレビューミーティングの実施
PDCAサイクルを確実に回すことで、継続的な改善を実現します。大塚商会の記事では、生産管理における継続的改善の重要性を強調しています。
4.4 従業員教育とチェンジマネジメント
生産計画最適化の成功には、従業員の理解と協力が不可欠です。適切な教育とチェンジマネジメントを実施することで、スムーズな導入を実現します。
4.4.1 効果的な従業員教育プログラム
- 新しい生産計画システムの操作研修
- データ分析スキルの向上トレーニング
- リーン生産方式の基本原則の理解
4.4.2 チェンジマネジメントのポイント
- 経営陣によるビジョンの明確な伝達
- 中間管理職の巻き込みと権限委譲
- 成功事例の共有と表彰制度の導入
従業員のエンゲージメント向上は、生産計画最適化の持続的な成功に不可欠です。中小企業庁によると、生産性向上に取り組む上で、評価、育成、配置等の人材マネジメントもモチベーションに直結するとされています。
以上のステップを着実に実施することで、効果的な生産計画の最適化を実現し、製造業の競争力強化につながります。重要なのは、継続的な改善と従業員の積極的な参加を促すことです。技術の進化と市場の変化に柔軟に対応しながら、最適化プロセスを進化させていくことが、長期的な成功の鍵となります。
5. 生産計画最適化の課題と対策
生産計画の最適化には多くの利点がありますが、実施にあたってはいくつかの課題も存在します。ここでは、主要な課題とその対策について詳しく見ていきます。
5.1 データの質と量の確保
生産計画の最適化には、正確で豊富なデータが不可欠です。しかし、多くの企業では以下のような課題に直面しています。
- データの不足や欠損
- データの信頼性の低さ
- 異なるシステム間でのデータの不整合
5.1.1 対策:
- データ収集プロセスの改善:自動化されたデータ収集システムの導入や、IoTデバイスの活用により、より正確で豊富なデータを収集します。
- データクレンジングの実施:定期的にデータの品質チェックを行い、不正確なデータを特定・修正します。
- データ統合プラットフォームの構築:異なるシステムからのデータを一元管理し、整合性を保ちます。
IBMによると、高品質のデータを活用することで、意思決定の精度が大幅に向上し、生産計画の最適化に大きく貢献します。
5.2 従業員のスキル向上と変化への適応
新しい生産計画最適化システムの導入には、従業員の適応が必要不可欠です。しかし、以下のような課題が生じることがあります:
- 新しいシステムへの抵抗感
- 必要なスキルの不足
- 変化に対する不安や懸念
5.2.1 対策:
- 包括的なトレーニングプログラムの実施:新システムの使用方法や利点について、段階的かつ実践的なトレーニングを提供します。
- 変更管理プロセスの導入:従業員の懸念や不安を積極的に聞き取り、対応策を講じます。
- 成功事例の共有:新システム導入による具体的な成果を社内で共有し、モチベーションを高めます。
McKinsey & Companyの調査によれば、従業員のスキル向上と変化への適応を支援することで、生産性が向上する可能性があります。
5.3 継続的な改善とイノベーション
生産計画の最適化は一度行えば終わりではなく、継続的な改善が必要です。しかし、以下のような課題が生じることがあります。
- 改善のための時間や資源の不足
- 新技術や手法の追跡の難しさ
- 組織全体での改善文化の欠如
5.3.1 対策:
- 定期的な評価と見直しの実施:KPIを設定し、定期的に生産計画の効果を測定・分析します。
- イノベーションラボの設置:新技術や手法を試験的に導入し、効果を検証する専門チームを設置します。
- 改善提案制度の導入:従業員からのアイデアを積極的に募集し、実装する仕組みを作ります。
アクセンチュアのレポートによると、製造業において卓越した成果をあげている企業は、デジタルを活用したイノベーションの拡大方法を見極め、高いデジタル投資収益率を上げているとのことです。
課題 | 主な対策 | 期待される効果 |
---|---|---|
データの質と量の確保 | データ収集プロセスの改善、データクレンジング、データ統合 | 意思決定の精度向上、生産計画の最適化 |
従業員のスキル向上と変化への適応 | トレーニングプログラム、変更管理プロセス、成功事例の共有 | 生産性の20〜30%向上 |
継続的な改善とイノベーション | 定期的な評価と見直し、イノベーションラボの設置、改善提案制度 | 競合他社の2倍以上の収益性 |
生産計画最適化の課題に適切に対処することで、企業は競争力を大幅に向上させることができます。データの質の向上、従業員のスキルアップ、そして継続的な改善文化の構築が、成功への鍵となります。これらの課題に真摯に取り組むことで、生産効率の向上、コスト削減、そして顧客満足度の向上といった多くの利点を享受することができるのです。
6. まとめ
生産計画の最適化は、製造業における競争力強化と効率性向上の鍵となります。本記事では、需要予測、在庫管理、生産スケジューリング、リソース配分など、最適化の主要要素を解説しました。
また、AIやIoT、クラウドシステムなどの先進技術の活用方法も紹介しました。トヨタ生産方式に代表される日本の製造業の強みを活かしつつ、デジタル化による更なる進化が求められています。
生産計画最適化の実施には、現状分析、戦略策定、段階的導入が重要です。データの質・量の確保や従業員のスキル向上など課題はありますが、継続的な改善努力によって克服できます。例えば、女性オフィスユニフォームやサービス・介護ユニフォームの企画・製造・販売を手がけるセロリー社では、AIを導入して生産計画策定の作業時間が10分の1に短縮されました。
生産計画の最適化は、製造業の未来を切り開く重要な取り組みと言えるでしょう。
product関連するプロダクト
-
UMWELTウムベルト
UMWELTは、プログラミング不要でかんたんに分析や自動化ができるノーコードツールです。需要予測から生産計画を最適化、人材の最適配置まで課題を解決できます。日々変化する生産数や生産計画、人員配置を自動立案し属人化や作業時間を大幅に削減します。
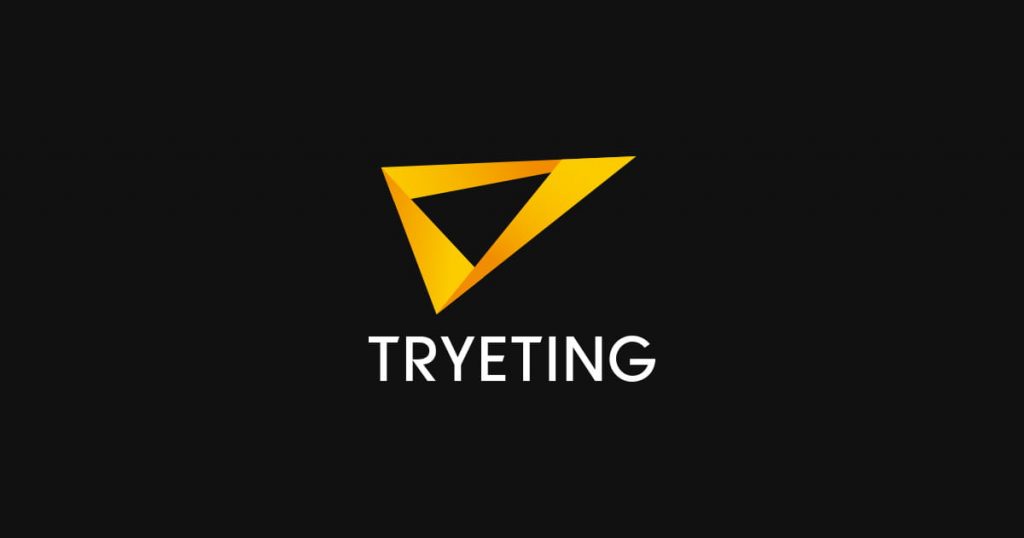
TRYETING
公式
TRYETING公式です。
お知らせやIR情報などを発信します。