BUSINESS
製造業のデジタルトランスフォーメーション4つの事例!手順やメリットを解説
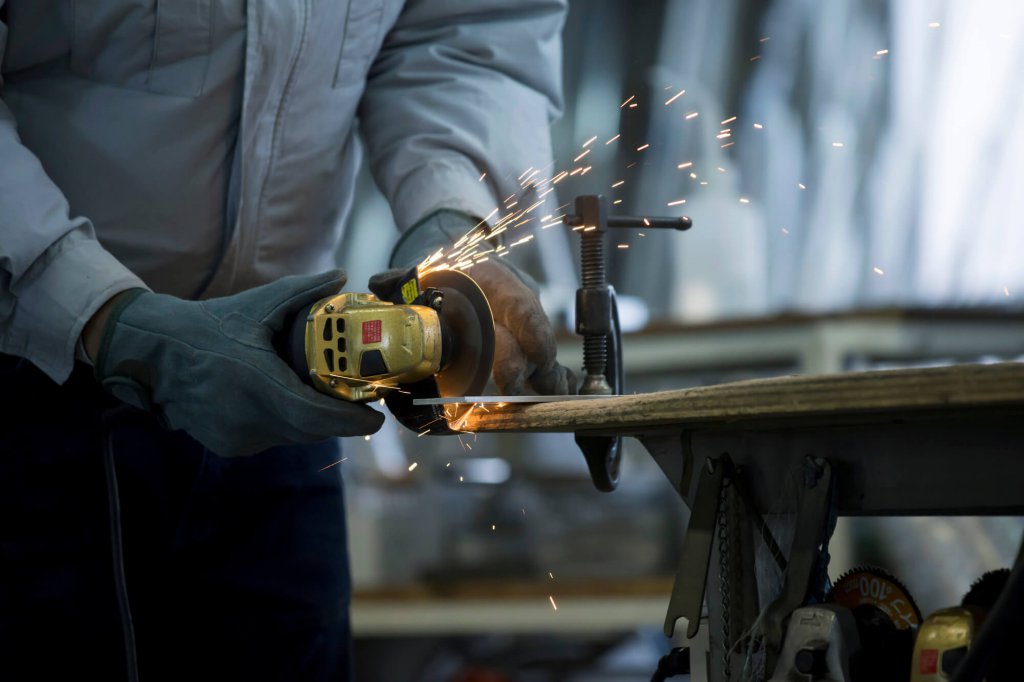
目次
デジタルトランスフォーメーション(DX)は、製造業をはじめさまざまな業界で取り組みが進んでいます。自社のデジタルトランスフォーメーション推進について考えているものの、どのような手順で進めればよいか分からない方もいるのではないでしょうか。
この記事では、製造業がデジタルトランスフォーメーションに取り組むメリットや事例を紹介します。最後まで読めば、デジタルトランスフォーメーションのイメージがつかめるでしょう。
製造業のデジタルトランスフォーメーションのメリット
デジタルトランスフォーメーションとは、ビジネスモデルやサービスをデジタル技術で改善・創出し、レガシーシステムから脱却することを意味します。
生産性の向上やコスト削減、新製品の開発など、デジタルトランスフォーメーションがもたらすメリットはさまざまです。ここでは、デジタルトランスフォーメーションのメリットを紹介します。
生産性の向上
IoTのようなデジタル技術の導入で効率が上がると、少ないリソースで安定的な品質と量をアウトプットできます。生産性の向上により確保した従業員やコストは、他の業務で活用が可能です。
製造業の生産性向上は、エネルギーや原材料にかかるコスト、設備を扱う従業員などのリソースを活用し、これまで以上の生産量を生み出すことを指します。労働力人口の減少が見込まれる日本にとって、生産性向上は大きなメリットです。
経費の軽減
製造や人材のコスト負担も製造業の課題のひとつです。人による確認作業をITツールで自動化すると、速度と精度は飛躍的に向上します。また、収集したデータの分析精度が高ければ、生産工程の合理化も進むでしょう。
デジタルトランスフォーメーションによって業務を効率化することで、人件費や生産コストを削減し、企業の収益性が向上します。
災害や緊急事態での事業の強化
新型コロナウイルス感染症のようなパンデミックや自然災害はいつ起きるか分かりません。万が一の事態に陥ったときでも、事業の継続は企業存続のために必要です。デジタルトランスフォーメーションは働き方を見直し、事業継続性を強化できます。
例えば、緊急事態の際に事業を継続するには、各拠点の従業員やサプライヤーと連絡を取って、生産停止を避けなくてはなりません。連絡手段としてデジタルトランスフォーメーションに関係するデジタルツールが必要です。
新しいビジネスモデルの創出
デジタルトランスフォーメーションを進めると、顧客のデバイスや機器に内蔵したIoTセンサーから得たデータの分析が可能です。
IoTとは、物とインターネットをつなぐ仕組みを指します。これまで埋もれていたデータを、サーバー上で処理・変換・分析・連携が可能です。IoTの情報からデータを分析し、商品の故障傾向や顧客ニーズが把握できます。
デジタル技術から得た情報を基に、新製品の開発やサービス改善、新たなビジネスの創出が期待できるでしょう。
属人化対策
属人化による問題は、特定の従業員に依存することで、必要な情報を他の従業員が把握できないことです。他にも、製品の品質差が発生する、不在時の対応ができないなどのデメリットが生じます。
デジタルトランスフォーメーションに関連するデジタル技術を活用することで、業務の標準化が可能です。どの従業員が作業しても、一定品質でアウトプットできます。
現場業務の見える化
デジタルトランスフォーメーションにより、製造業の業務プロセス全体を「見える化」できます。受注からアフターサービスまで全工程をデジタル化すれば、生産工程や設備の状況に関するデータが一元化できるでしょう。
例えば、作業手順をマニュアル化すると、従業員が何に取り組んでいるのか簡単に把握できます。見える化は、業務中のトラブルを素早く検知できる他、未然に防げる点がメリットです。
デジタルトランスフォーメーションとデジタル化の違いとは
デジタルトランスフォーメーションとデジタル化はどちらもデジタル技術を使いますが、目的が異なります。デジタルトランスフォーメーションを正しく進めるためにも、両者の違いを理解しましょう。
ここでは、デジタルトランスフォーメーションとデジタル化の違いを解説します。
デジタルトランスフォーメーションの目的
デジタルトランスフォーメーションの目的は、AIやIoTなどのデジタル技術を活用して社会全体を変革することです。
製造業におけるデジタルトランスフォーメーションの目的は、製品やサービスの顧客価値を高め、企業が競争上の優位性を維持し続けることです。AIや他のデジタル技術を駆使して業務を効率化し、組織全体の生産性の向上を目指します。
これまでの製造業は、職人の技術や伝統的な生産技術を重視し、企業の価値を支えてきました。しかし、社会が急速にデジタル化を進める中、経営の維持は困難になりつつあります。製造業におけるデジタルトランスフォーメーションは、早急な対応が必要です。
デジタル化は既存の作業をデジタルに置き換えること
デジタル化は、既存のアナログ作業をデジタル技術によって置き換え、業務の効率化と生産性の向上を図ることです。
かつては電話・ファックス・書類などが主要な情報伝達手段でしたが、現在はメール・チャット・ビデオ会議システムといったデジタルコミュニケーション手段が多様化しています。これにより、時間や場所の制約がなくなりました。
業務の自動化やデータの効率的な管理により、従来のプロセスに比べて時間とコストを削減できます。
デジタル化の事例
デジタル化の事例は以下の通りです。
・ビジネスチャットツールの導入
手軽に意思疎通が図れるため、業務が円滑になります。
・オンライン会議システムの導入
会議や商談をオンライン上でできるため、会議室の確保や移動が不要です。
・電子契約の導入
オンライン上で契約書作成や電子署名が可能で、印刷や郵送にかかるコストの削減とペーパーレス化が実現します。
・クラウドサービスの導入
クラウドサービスは、ネットワーク経由で業務に必要なアプリケーションやデータを利用するサービスです。業務のデジタル化と情報管理の推進が図れます。
製造業のデジタルトランスフォーメーション4つの事例
製造業においても、デジタルトランスフォーメーションにより成果を挙げている企業があります。事例を見ることで、自社でどのような取り組みができるか参考になるでしょう。
ここでは、デジタルトランスフォーメーションの事例を4つ紹介します。
「バーチャル・ワンファクトリー」沖電気工業株式会社
沖電気工業株式会社は、マスカスタマイゼーションのニーズや社会変化による需要減への対応として、デジタルトランスフォーメーションを推進しています。以前は、工場ごとに技術標準に差があり、同一仕様の生産ができない状況でした。
課題を解決するため、「バーチャル・ワンファクトリー」の概念を導入して、工場間の連携強化を図りました。具体的には、2つの工場の生産高を維持しながら効率化を進めるとともに、人材や技術の交流を活発化する取り組みです。
その結果、技術の共通化だけでなく、両拠点の強みを生かした生産体制を実現しました。2工場を連携したことで、多品種少量生産ニーズや人手不足にも対応できます。
「FTCP(設計開発プラットフォーム)」富士通株式会社
富士通株式会社は、製品のカスタマイズ化への対応、納期の短縮、製品の複雑化・高密度化への対応、管理コスト、技術の伝承、人手不足といった課題がありました。
これらの課題解決のため取り組んだのが「FTCP(設計開発プラットフォーム)」の導入です。FTCPは、デジタルモックアップ技術や3D-CAD、エレキCADで構成されています。
FTCPを導入したことで、試作品を作らずに干渉具合やデザインが確認できるようになった他、製品開発に関する知見の共有やコミュニケーションの円滑化に成功しました。
デジタル化によって設計段階の不具合抽出や製造しやすい設計の追求が可能となり、手戻りの減少や品質の向上、納期の短縮といった成果を得ています。
「工場IoT」トヨタ自動車株式会社
トヨタ自動車株式会社は、製造現場や顧客から得たデータを技術開発へタイムリーにフィードバックできない課題がありました。
デジタル技術を活用したトヨタ生産方式の一環として、従業員が小規模なテーマを立案・実行し、効果を出すボトムアップの取り組みを進めました。
まずは生産部門と連携し、「工場IoT」のプラットフォームを準備します。各事業部や工場で現場プロジェクトを立ち上げ、取り組みの数を増やすことで、トータルで費用対効果を高めました。
工場IoTによって得た成果を受け、エンジニアリングチェーンやサプライチェーンを含むデジタル化への適用を考案します。これにより、品質や商品力の向上、法規への対応といった付加価値向上に関わるデジタル化が始まりました。
「社内人材のデジタル人材としての育成」株式会社IHI
株式会社IHIは幅広い事業を展開しており、各事業部でIoTを用いた個別のデジタル化を進めています。以前はデータをどのように活用するかという課題を抱えていました。個別最適化した事業間の統合を行うため、高度情報マネジメント統括本部を設置しています。
取り組みの一環として、デジタル変革に関与する人材を社内公募し、さまざまな部門や製品カテゴリーのビジネスユニットから人材を集めました。さらに、事業部門を対象にデジタル人材育成プログラムにも着手します。
業務知識が豊富な人材を集めたことで、多様なアイデアが出せる環境の構築に成功しました。
製造業でデジタルトランスフォーメーションを導入する流れ
製造業のデジタルトランスフォーメーションへの取り組みは、企業の競争力を高め、ビジネスの成長を促進します。
しかし、デジタルトランスフォーメーションを推進するには計画的なアプローチが必要です。ここでは、デジタルトランスフォーメーションを進める流れを紹介します。
体制の整備
デジタルトランスフォーメーションを進める際は、改善したい課題を明確にし、ビジョンを共有しましょう。現場で抱える問題点を見つけるには、組織全体の共有が大切です。具体的な課題から戦略を立てることで、目指す方向を明らかにします。
デジタルトランスフォーメーションの推進は、会社全体のプロジェクトです。部門ごとに進めるのではなく、経営陣を中心とする体制を整備しましょう。
データを分析
デジタルトランスフォーメーションには、目的達成に必要なデータの収集と分析が欠かせません。何のデータが必要か、データをどのように活用するか、市場ニーズを組み込みながら検討します。
データ分析は専門的な技術が求められるため、ITリテラシーを持った人材の確保や外部コンサルティングによるサポートが必要になるケースもあります。データ分析の結果は常に見直して、運用を通じてデータの信頼性を高めましょう。
システムの導入
データの分析と活用の方法が決まったら、AIなどのITシステムを導入して業務の効率化を図りましょう。全ての業務を一度にシステム化すると、従業員が混乱するリスクがあります。導入は少しずつ進め、タイミングを見計らって拡大するとよいでしょう。
段階的な導入により、システムが業務フローに適切に組み込まれて、企業全体の効率化と競争力強化を実現します。
製造業のDXはノーコードAIツールUMWELTにお任せください!
デジタルトランスフォーメーションの推進には、TRYETINGの『UMWELT』がおすすめです。UMWELTは、効率的な在庫管理や需要予測を実現するノーコードAIツールで、Excelのような日常業務で使うデータを利用できます。
専門知識がなくとも操作できる点も魅力です。新たな人材を確保することなく、デジタルトランスフォーメーションに取り組めます。
まとめ
製造業におけるデジタルトランスフォーメーションには、組織体制の見直しや適切なデータ分析が欠かせません。さまざまな方法がありますが、コスト削減や業務効率化を実現するデジタルツールの導入をおすすめします。
TRYETINGのUMWELTは、AIやプログラミングに関する専門知識は不要です。業務効率化に成功した製造業の事例もあります。無料相談もありますので、お気軽にお問い合わせください。
product活用したプロダクト
-
UMWELTウムベルト
UMWELTは、プログラミング不要でかんたんに分析や自動化ができるノーコードツールです。需要予測から生産計画を最適化、人材の最適配置まで課題を解決できます。日々変化する生産数や生産計画、人員配置を自動立案し属人化や作業時間を大幅に削減します。
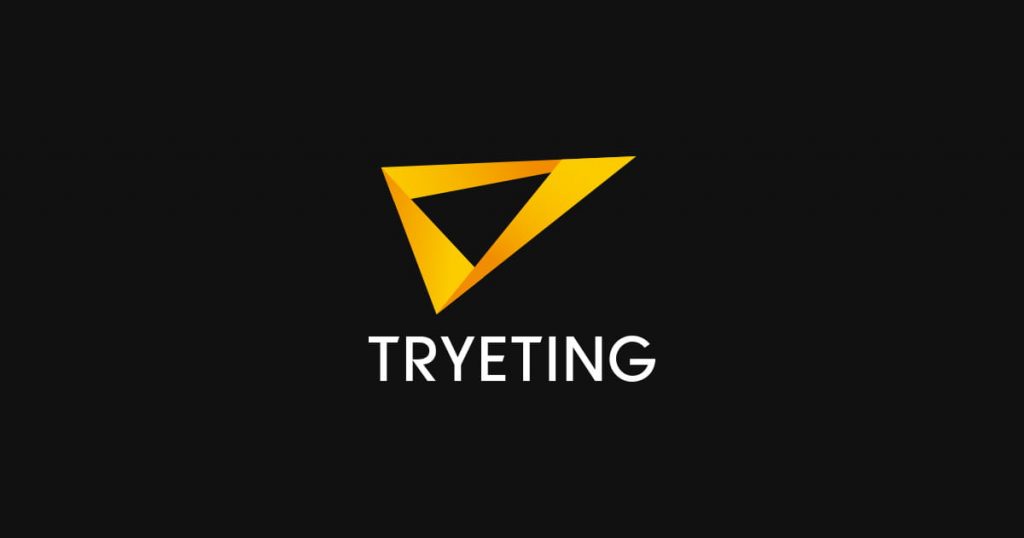
TRYETING
公式
TRYETING公式です。
お知らせやIR情報などを発信します。