BUSINESS
メーカーの生産効率を120%に!最適化のための具体的な手順と成功事例
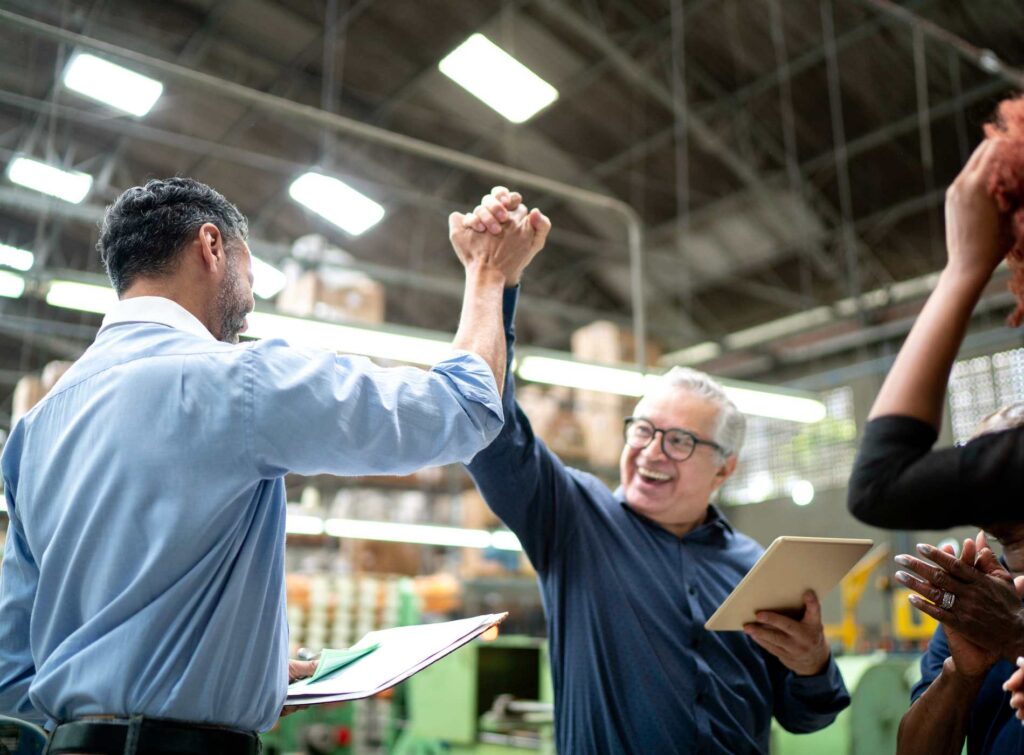
目次
製造業における生産効率の向上は、企業の競争力を左右する重要な課題です。
本記事では、トヨタ生産方式やカンバン方式といった日本発の生産管理手法から、オムロンやファナックが展開する最新のIoTソリューションまで、具体的な最適化手法を網羅的に解説します。パナソニックや日立製作所、デンソーなど、実際に生産性を向上させた企業の事例も交えながら、現状分析から導入後のPDCAサイクルまで、段階的な実施手順を詳しく紹介。設備稼働率の向上、在庫の適正化、品質管理の安定化など、製造現場が抱える課題への具体的な解決策が分かります。
経営者から現場責任者まで、製造業に携わるすべての方に役立つ実践的な情報を提供します。
1. 製造業における生産最適化の重要性
製造業を取り巻く環境は、グローバル競争の激化や労働人口の減少、原材料価格の高騰など、年々厳しさを増しています。そのような状況下で、企業が持続的な成長を実現するためには、生産効率の最適化が不可欠となっています。
生産最適化のメリットは以下の3点に集約されます。
1. コスト削減効果:製造プロセスの効率化により、原材料のロスや人件費、エネルギーコストを平均して15-20%削減することが可能です。
2. 品質向上:自動化とデータ分析により、不良品率を従来比50%以上削減できた事例が多数報告されています。
3. リードタイム短縮:工程の最適化により、受注から納品までの期間を平均30%短縮することが可能です。
特に注目すべきは、経済産業省が推進するDXを活用したスマートファクトリー化です。IoTやAIの導入により、従来の生産方式では実現できなかった柔軟な生産体制の構築が可能となっています。
一方で、最適化に向けた投資は、単なるコスト削減だけでなく、従業員の労働環境改善にも貢献します。経産省によれば、生産最適化を実施した企業の従業員満足度が向上する可能性が示唆されています。
このように、製造業における生産最適化は、企業の競争力強化と持続可能な成長を実現するための戦略的な取り組みとして、その重要性がますます高まっているのです。
2. 生産最適化で解決できる5つの課題
製造業における生産最適化は、複数の重要な経営課題を同時に解決することが可能です。ここでは、多くのメーカーが直面している5つの主要な課題について詳しく解説します。
2.1 生産リードタイムの長期化
生産リードタイムの長期化は、顧客ニーズへの迅速な対応を妨げ、市場競争力の低下につながる深刻な問題です。
主な原因 | 影響 | 改善の方向性 |
---|---|---|
工程間の待ち時間 | 納期遅延 | 工程の同期化 |
段取り替え時間の長さ | 生産効率低下 | 段取り時間の短縮 |
非効率な作業動線 | 作業時間増加 | レイアウト最適化 |
2.2 在庫管理の非効率性
在庫の過不足は企業の収益性に直接影響を与えます。過剰在庫は保管コストと資金繰りを圧迫し、在庫不足は機会損失を招くという両面のリスクがあります。
経済産業省の工業統計調査によると、製造業の在庫率は業種によって大きく異なり、最適な在庫水準の設定が課題となっています。
2.3 設備稼働率の低下
設備稼働率の低下は、直接的な生産性低下につながります。計画外の設備停止や不適切なメンテナンス計画が主な原因となっており、設備投資効率の悪化を引き起こしています。
2.4 品質管理の不安定さ
品質のばらつきや不良品の発生は、顧客満足度の低下だけでなく、補償コストや風評被害などの二次的な損失も生む重大な問題です。
日本能率協会によると、品質管理体制の整備が不十分な企業が依然として多く存在することが指摘されています。
2.5 人的リソースの無駄
人的リソースの非効率な活用は、労働生産性の低下と従業員のモチベーション低下を引き起こします。特に熟練工の技能伝承や作業の標準化が遅れている企業では、この問題が顕著に表れています。
無駄の種類 | 発生要因 | 改善アプローチ |
---|---|---|
待機時間 | 工程間の連携不足 | 多能工化の推進 |
重複作業 | 作業分担の不明確さ | 役割の明確化 |
過剰な動作 | 作業環境の非効率 | 動作経済の原則適用 |
3. メーカーの生産最適化を実現する3つの手法
製造業における生産最適化を実現するため、現在主流となっている3つの手法について詳しく解説します。これらの手法を適切に組み合わせることで、生産効率の大幅な向上が期待できます。
3.1 工程管理システムの導入
工程管理システムは、製造現場の可視化と効率化を実現する基盤となるシステムです。生産計画から実績管理まで、一貫した管理を可能にします。
3.1.1 トヨタ生産方式の活用
トヨタ生産方式(TPS)は、ムダを徹底的に排除する生産方式として世界的に認められています。「ジャストインタイム」と「自働化」という2つの柱を中心に、継続的な改善を行うことで生産効率を向上させます。
TPS要素 | 目的 | 効果 |
---|---|---|
ジャストインタイム | 必要なものを必要な時に必要な量だけ生産 | 在庫削減、リードタイム短縮 |
自働化 | 異常時に機械が自動停止 | 品質向上、不良品削減 |
3.1.2 カンバン方式の実装
カンバン方式は、生産工程間の情報伝達を視覚的に行う手法です。デジタルカンバンの導入により、リアルタイムでの進捗管理と工程間の同期が可能になります。
3.2 IoTセンサーによる設備監視
製造設備にIoTセンサーを設置することで、稼働状況をリアルタイムで把握し、予防保全を実現します。
3.2.1 オムロンの予知保全システム
オムロンのi-BELTは、製造現場のデータを収集・分析し、設備の異常を事前に検知します。AIによる予測分析により、設備の故障を未然に防ぎ、ダウンタイムを最小限に抑えることが可能です。
3.2.2 ファナックのAIサービス
ファナックのFIELDsystemは、工作機械やロボットの稼働データを収集・分析し、生産性向上を支援します。エッジヘビー型のAIプラットフォームにより、リアルタイムでの異常検知と最適制御を実現します。
3.3 デジタルツイン技術の活用
デジタルツイン技術は、現実の製造設備やプロセスをデジタル空間に再現し、シミュレーションを可能にします。仮想環境での検証により、実際の製造現場でのリスクを最小限に抑えながら、最適な生産条件を見出すことができます。
活用分野 | 主な機能 | 期待効果 |
---|---|---|
製造ライン設計 | レイアウト最適化 | スペース効率向上 |
工程シミュレーション | ボトルネック分析 | 生産性向上 |
品質管理 | 不良要因分析 | 歩留まり改善 |
4. 生産最適化の具体的な導入ステップ
製造業における生産最適化を成功させるためには、体系的なアプローチが不可欠です。ここでは、具体的な導入ステップを詳しく解説します。
4.1 現状分析と課題抽出
最適化を始める前に、まず現状を正確に把握する必要があります。
分析項目 | チェックポイント | 使用ツール |
---|---|---|
生産性分析 | 時間当たり生産量、歩留まり率 | 生産管理システム |
品質分析 | 不良率、手直し工数 | 品質管理表 |
コスト分析 | 原材料費、労務費、経費 | 原価計算システム |
データに基づく現状分析により、以下の要素を明確化します。
- 生産ラインのボトルネック
- 品質上の課題点
- 在庫管理の非効率性
- 設備稼働率の実態
4.2 最適化目標の設定
現状分析に基づき、具体的な数値目標を設定します。
目標設定では、SMART原則(Specific:具体的、Measurable:測定可能、Achievable:達成可能、Relevant:関連性、Time-bound:期限付き)に従うことが重要です。
項目 | 現状値 | 目標値 | 達成期限 |
---|---|---|---|
生産効率 | 80% | 95% | 6ヶ月 |
不良率 | 2% | 0.5% | 3ヶ月 |
在庫回転率 | 12回/年 | 24回/年 | 12ヶ月 |
4.3 導入計画の策定
目標達成のための具体的な実行計画を策定します。
- 責任者とチーム編成の決定
- タイムラインの作成
- 必要リソースの算出
- リスク分析と対策立案
4.4 パイロット運用と効果測定
特定のラインや工程で試験的に導入を行い、効果を検証します。
パイロット運用では、以下の3点に注目して効果を測定します。
- 生産性向上率
- 品質改善度
- コスト削減効果
4.5 本格展開とPDCAサイクル
パイロット運用の結果を踏まえ、全社的な展開を行います。
PDCAサイクルを確実に回すことで、継続的な改善を実現します。
PDCAステップ | 実施項目 | 頻度 |
---|---|---|
Plan | 月次目標設定 | 月1回 |
Do | 改善活動実施 | 日次 |
Check | 実績評価 | 週1回 |
Act | 改善策検討 | 月1回 |
生産最適化の成功には、現場の意見を積極的に取り入れながら、データに基づいた継続的な改善活動を実施することが不可欠です。
5. 日本の製造業における最適化成功事例
製造業における生産最適化の取り組みは、日本国内でも着実に成果を上げています。ここでは、特に顕著な成果を上げている企業の事例を詳しく見ていきましょう。
5.1 パナソニックの生産ライン改革
パナソニックは草津工場において、IoTなどを活用したスマートファクトリー化を実現し、生産効率を向上させることに成功しました。
5.2 日立製作所のスマートファクトリー
日立製作所の大みか事業所では、Lumada(ルマーダ)を活用したデジタル改革により、製造リードタイムを短縮し、生産性を向上させました。
主な取り組みには以下が含まれます:
- 作業員の動線分析による工程配置の最適化
- リアルタイムでの進捗管理システムの構築
- 予知保全による設備停止時間の削減
5.3 デンソーの自動化システム導入
デンソーは愛知県西尾市の工場に「24時間無人稼働の次世代工場」を建設することを発表。デジタルをフル活用して、大規模統合ECUの生産を行います。
6. 生産最適化における注意点と課題
生産最適化を成功に導くためには、いくつかの重要な注意点と潜在的な課題に着目する必要があります。ここでは、主要な3つの観点から詳細に解説します。
6.1 従業員教育の重要性
生産最適化システムの導入は、従業員の理解と適切な運用なくしては成功しません。以下に、効果的な従業員教育のポイントをまとめます。
教育項目 | 具体的な内容 | 実施頻度 |
---|---|---|
基礎研修 | システムの基本操作と理念理解 | 導入時および四半期ごと |
専門研修 | トラブルシューティングと改善提案 | 半年ごと |
リーダー育成 | マネジメントスキルと分析手法 | 年1回 |
6.2 コスト管理の考え方
生産最適化に伴うコストは、短期的な投資と長期的な運用コストの両面から検討する必要があります。初期投資を抑えるために必要な機能を削減すると、かえって長期的なコストが増大するリスクがあります。
日本能率協会コンサルティングの調査によると、最適化プロジェクトの成功のためには、従業員教育に力を入れることが重要とされています。
6.3 段階的な導入のすすめ
一度に全工程の最適化を目指すのではなく、段階的なアプローチを取ることが重要です。パイロットラインでの実証を経て、成功事例と課題を明確にしてから展開することで、リスクを最小限に抑えることができます。
導入フェーズ | 期間 | 主な実施事項 |
---|---|---|
準備期 | 3ヶ月 | 現状分析・計画策定 |
パイロット期 | 6ヶ月 | 一部ラインでの試験導入 |
展開期 | 1年 | 全社展開・改善活動 |
経済産業省の製造業DXガイドラインでも、段階的な導入の重要性が指摘されています。特に中小製造業においては、投資対効果を見極めながら慎重に進めることが推奨されています。
また、最適化プロジェクトの成否を分けるのは、現場の声を活かした改善サイクルの確立です。定期的な効果測定と改善提案の仕組みを構築することで、持続的な生産性向上を実現できます。
7. まとめ
メーカーの生産最適化は、トヨタ生産方式やカンバン方式などの日本発の手法を基本としながら、最新のIoT技術やデジタルツイン技術を組み合わせることで、大きな効果を生み出すことが可能です。パナソニックや日立製作所、デンソーなどの事例が示すように、段階的な導入と従業員教育の充実が、生産性向上の鍵となります。
特に工程管理システムの導入では、オムロンやファナックのAIソリューションを活用することで、予知保全や品質管理の精度を向上させることができます。ただし、急激な自動化や過度なシステム依存は逆効果となる可能性があるため、現場の状況に応じた適切なペースでの導入が推奨されます。
人材育成とデジタル技術の調和を図りながら、継続的な改善活動を実施することで、生産効率を高めることは十分に実現可能です。
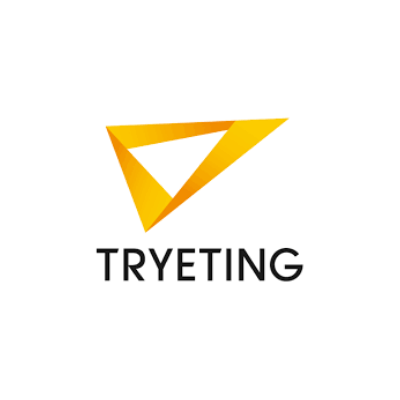
TRYETING
編集部
TRYETING編集部です。
記事の更新を進めてまいります。